How to Figure Out COGS: A Step-by-Step Guide

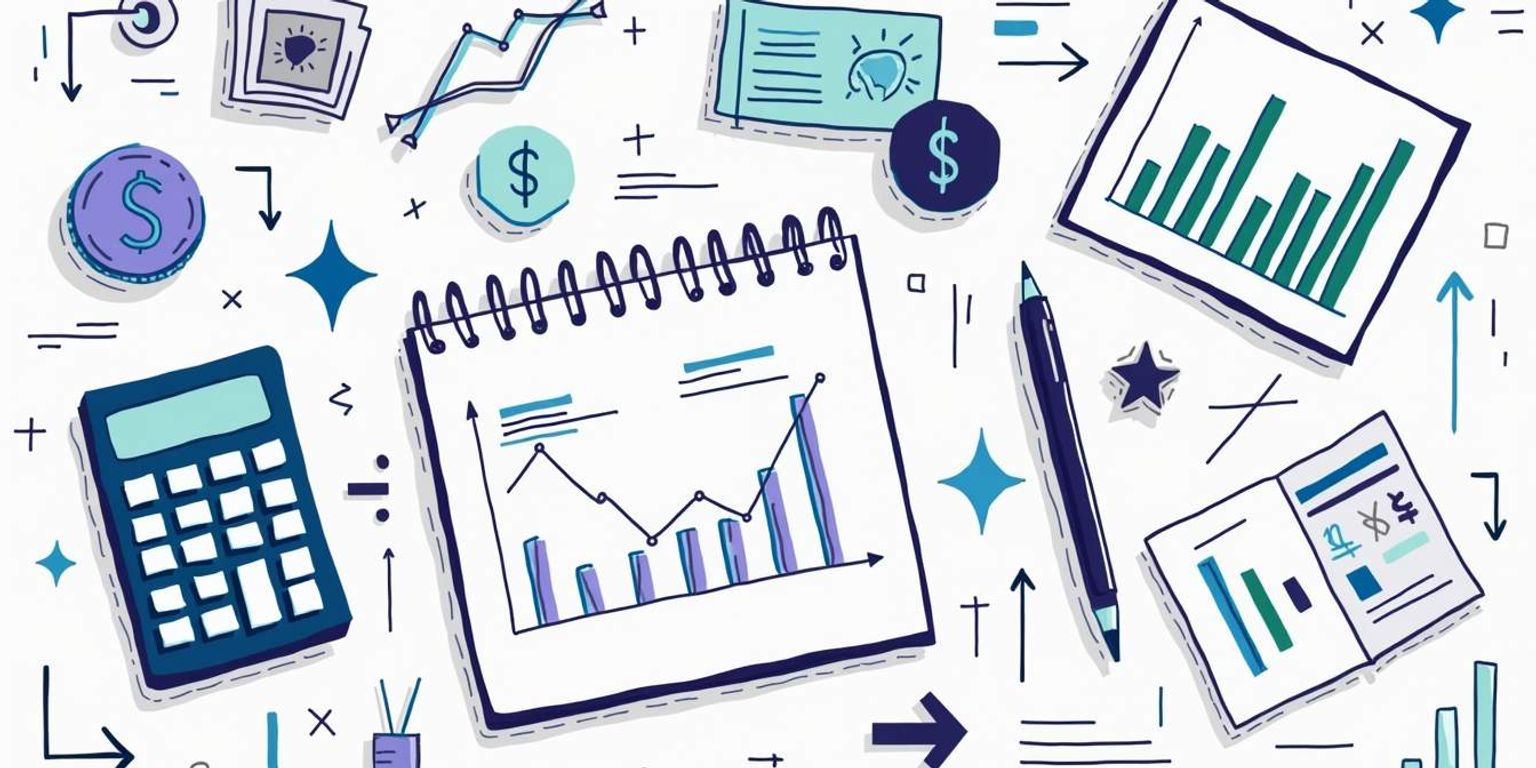
How to Figure Out COGS: A Step-by-Step Guide
Understanding the Cost of Goods Sold (COGS) is crucial for any business that sells products. It directly impacts profitability and pricing strategies. This guide will walk you through the process of calculating COGS step-by-step, ensuring you have a solid grasp of this important financial metric.
What is COGS?
Cost of Goods Sold (COGS) represents the direct costs attributable to the production of the goods sold by a company. This includes the cost of materials and labor directly used to create the product. Understanding COGS is essential for determining gross profit and overall financial health. It serves as a fundamental metric that businesses must track to ensure they are operating efficiently and effectively.
COGS does not include indirect expenses such as sales and marketing costs, which are accounted for separately. By isolating the direct costs associated with production, businesses can better understand their profitability and make informed decisions about pricing and inventory management. For instance, a company that can accurately calculate its COGS will be in a better position to forecast future expenses and manage cash flow, which is critical for sustaining operations and growth.
Importance of COGS
COGS plays a pivotal role in financial reporting and analysis. It is a key component of the income statement and is used to calculate gross profit. A lower COGS can lead to higher gross profits, which can be reinvested into the business or distributed to shareholders. Additionally, a thorough analysis of COGS can reveal trends over time, allowing businesses to identify areas where they can cut costs or improve efficiency, ultimately leading to enhanced operational performance.
Moreover, understanding COGS helps businesses in pricing their products effectively. By knowing the exact cost of producing a product, companies can set prices that cover costs and generate profit while remaining competitive in the market. This strategic pricing is crucial, especially in industries with thin margins, where even slight fluctuations in COGS can significantly impact overall profitability. Furthermore, businesses that regularly review and analyze their COGS can adapt to changes in supplier pricing or shifts in production processes, ensuring they maintain a competitive edge while safeguarding their bottom line.
Components of COGS
To accurately calculate COGS, it’s essential to identify all the components that contribute to the cost of goods sold. These typically include direct materials, direct labor, and manufacturing overhead.
Direct Materials
Direct materials are the raw materials that are used to create a product. For example, if a company manufactures furniture, the wood, fabric, and hardware used in production would be considered direct materials. Keeping track of these costs is vital for an accurate COGS calculation.
Businesses often maintain inventory records to monitor the cost of materials. This can include purchase prices, shipping costs, and any other expenses incurred to acquire the materials necessary for production. Additionally, companies may implement inventory management systems that utilize just-in-time (JIT) methodologies to minimize waste and reduce holding costs, ensuring that materials are available when needed without overstocking. This strategic approach not only aids in cost control but also enhances operational efficiency.
Direct Labor
Direct labor refers to the wages paid to employees who are directly involved in the production of goods. This includes workers on the assembly line, machine operators, and anyone else whose labor contributes directly to the creation of the product.
Calculating direct labor costs can involve tracking hours worked and multiplying by hourly wages. Accurate timekeeping and payroll systems are essential for determining these costs effectively. Furthermore, businesses may also consider overtime pay and benefits as part of direct labor costs, which can significantly impact the overall expense. By investing in robust workforce management tools, companies can optimize labor allocation, reduce inefficiencies, and ensure that labor costs are aligned with production demands.
Manufacturing Overhead
Manufacturing overhead includes all the indirect costs associated with production that cannot be directly traced to a specific product. This can encompass utilities, rent for the manufacturing facility, and depreciation of equipment.
Allocating manufacturing overhead can be complex, but it is necessary for a complete COGS calculation. Many businesses use a predetermined overhead rate based on estimated costs and production levels to simplify this process. In addition, companies may conduct regular reviews of their overhead costs to identify areas for potential savings, such as energy efficiency upgrades or renegotiating lease terms. Understanding the nuances of overhead allocation not only aids in pricing strategies but also plays a critical role in financial forecasting and budgeting, ensuring that a company remains competitive in its market.
Calculating COGS: Step-by-Step Process
Now that the components of COGS are clear, let’s dive into the step-by-step process of calculating it. This involves gathering data from inventory records, financial statements, and production reports.
Step 1: Determine Beginning Inventory
Beginning inventory is the value of inventory at the start of the accounting period. This figure can be found on the previous period’s balance sheet. It is essential to have an accurate beginning inventory to ensure the COGS calculation is correct.
For businesses that maintain consistent inventory records, this figure should be readily available. If inventory levels fluctuate significantly, it may be necessary to conduct a physical inventory count to determine the accurate beginning balance.
Step 2: Add Purchases During the Period
The next step is to add any purchases made during the accounting period to the beginning inventory. This includes all materials and goods acquired for production. Keeping detailed records of purchases, including invoices and receipts, is vital for this step.
It’s important to consider any returns or discounts that may affect the total purchases. Adjusting for these factors ensures that the calculation reflects the true cost of goods available for sale.
Step 3: Calculate Ending Inventory
Ending inventory is the value of inventory remaining at the end of the accounting period. This figure can be determined through a physical inventory count or by using inventory management software. Accurate inventory tracking is crucial for determining COGS.
Once the ending inventory is established, it will be subtracted from the total cost of goods available for sale to arrive at the COGS figure.
Final COGS Calculation
With all the necessary components gathered, the final COGS calculation can be performed using the following formula:
COGS = Beginning Inventory + Purchases - Ending Inventory
By plugging in the numbers, businesses can arrive at the COGS figure for the accounting period. This figure will be critical for preparing financial statements and analyzing profitability.
Example Calculation
To illustrate the COGS calculation, consider a hypothetical company with the following figures:
- Beginning Inventory: $10,000
- Purchases During the Period: $20,000
- Ending Inventory: $5,000
Using the formula, the calculation would be as follows:
COGS = $10,000 + $20,000 - $5,000 = $25,000
This means the cost of goods sold for the period is $25,000, which will be used to determine gross profit and other financial metrics.
Tracking COGS Over Time
Once COGS has been calculated, it’s essential to track this metric over time. monitoring COGS can provide valuable insights into production efficiency, cost control, and pricing strategies.
Analyzing Trends
By analyzing trends in COGS, businesses can identify areas for improvement. For instance, if COGS is increasing disproportionately compared to sales, it may indicate rising material costs or inefficiencies in production.
Regularly reviewing COGS can help businesses make informed decisions about pricing, sourcing materials, and optimizing production processes. This proactive approach can lead to improved profitability and competitiveness in the market.
Utilizing Technology for COGS Tracking
Modern businesses can leverage technology to streamline COGS tracking. Inventory management software and accounting systems can automate calculations and provide real-time insights into costs.
For example, Clarify is building a next-generation CRM that integrates seamlessly with inventory management tools, allowing businesses to track COGS more efficiently. By utilizing such technology, companies can focus on strategic decision-making rather than manual calculations.
Common Mistakes to Avoid
When calculating COGS, businesses should be aware of common pitfalls that can lead to inaccuracies. Avoiding these mistakes can ensure a more precise financial picture.
Neglecting Indirect Costs
One common mistake is neglecting to include all relevant indirect costs in the COGS calculation. While COGS focuses on direct costs, failing to account for necessary overhead can lead to an inflated gross profit figure.
It’s crucial to have a comprehensive understanding of all costs associated with production to ensure accurate reporting. Regular audits of cost components can help identify any overlooked expenses.
Inaccurate Inventory Counts
Inaccurate inventory counts can significantly impact COGS calculations. If beginning or ending inventory figures are incorrect, it can lead to erroneous COGS results.
Implementing regular inventory audits and utilizing technology for tracking can help mitigate this risk. Ensuring that inventory records are up-to-date and accurate is essential for reliable COGS calculations.
Ignoring Seasonal Variations
Many businesses experience seasonal fluctuations in sales and production. Ignoring these variations can lead to misleading COGS figures.
It’s important to analyze COGS in the context of seasonal trends. This can help businesses adjust their production and inventory strategies to align with expected demand, ultimately improving profitability.
Conclusion
Understanding and calculating COGS is a fundamental aspect of managing a successful business. By following the step-by-step process outlined in this guide, companies can gain valuable insights into their production costs and overall profitability.
Regularly tracking COGS and analyzing trends can lead to informed decision-making, helping businesses optimize their operations and pricing strategies. With the right tools and practices in place, such as those offered by Clarify, organizations can enhance their financial management and drive growth.
In summary, COGS is not just a number; it’s a vital indicator of a company’s operational efficiency and financial health. By mastering COGS calculations and avoiding common pitfalls, businesses can position themselves for long-term success.
Take Control of Your COGS with Clarify
Ready to elevate your business's financial health and operational efficiency? Clarify is here to streamline your COGS tracking and provide the insights you need to thrive. Our AI-powered CRM is designed to simplify complex processes, giving you more time to focus on strategic growth. Don't let manual calculations hold you back. Request access to Clarify today and experience the future of customer relationship management.
Get our newsletter
Subscribe for weekly essays on GTM, RevTech, and Clarify’s latest updates.
Thanks for subscribing! We'll send only our best stuff. Your information will not be shared and you can unsubscribe at any time.